The end of life of textiles is creating a huge cost that no one is bearing right now. Only strict EPR in which textile industries take back or pay for storage or own the end of life costs will this very problematic textile waste be treated in a more sustainable manner.
This is the second of a two part series on the mounting textile waste that Bangalore generates and the various issues in disposing-recycling-reusing them. The first part can be read here.
The current destinations for textile waste, post sorting at DWCCs are
- Clothes in wearable conditions are first used by the sorters at the DWCC
- The rest are sold in low income communities or construction workers’ camps, and to textile waste aggregators.
- Some of the soiled clothes are given to the BBMP compactor drivers who collect cloth waste from DWCCs and pack the door of the compactor so the leachate from the mixed waste compacted can be absorbed to avoid leaking on the road during the journey to landfills or quarries
- The rest of the non-reusable textile waste is sent to cement kilns for co-processing.
The experience in managing large amounts of cloth waste
Collection: The lack of systematic collection of textile waste, as a separate stream makes it very difficult to find a market for reusable textiles.
Mixed collection with dry waste: Textile waste mixed with dry waste collection streams further compounds the problem, as even usable garments are soiled and dirty, and often end up in waste dumping yards.
Diversity in blend of textiles: The diversity and heterogeneity of textiles makes it difficult to process or dispose and ends up as Refuse-Derived Fuel (RDF) in co processing units or is dumped in landfills.
Informal supply chains: Bengaluru had a long tradition of a barter system for cloth waste. The itinerant buyers would go door to door and collect reusable clothes and sarees with zari borders and in exchange would give steel kitchen utensils, later moved to plastic utensils. As the housing pattern changed from individual homes to housing complexes, there was reduced access to consumers for the itinerant buyers. Now, they go to known areas, DWCCs and buy clothes per garment or by weight. These are sorted, cleaned and sold. The markets that are available to the traders are Sunday markets like in BVK Iyengar Road. If they get a large consignment they sell the clothes on pavements at these markets. One of the largest markets is construction workers camps. Traders go from one camp to another on Sundays to sell their cleaned garments.
Read more: The what, why and how of a plastic waste brand audit
Incomplete solutions: Almost all post-consumer non-reusable textile waste ends up either in landfills or as part of RDF (Refuse Derived Fuel) that works as a small percentage of replacement for coal or natural gas. This is economically not feasible as the cement kilns are far from Bengaluru. Clothes are mixed with other combustible fragments from waste like non- recyclable plastics, multi-layered plastic (MLP), rexine, old furniture etc. In reality, clothes are not efficient for co-processing because of their low calorific value compared to other combustible fragments. A sustainable circular economy strategy such as investments in technology to recover yarn from garments and reuse it in textiles would be a preferred method.
Imported textiles preferred: Textile waste recyclers and associations of recyclers indicate their general preference for input feed from imported, clean, segregated cloth waste, post-production waste, and post-consumer clean reusable waste. Small and medium entrepreneurs pick up post production waste that is used as filling for beds and pillows. They are reluctant to use post-consumer waste out of fear of non-acceptance by customers’ of used clothes and the changes in their own production system. This in turn results in no takers other than landfills/dump yards and incinerators. Most recyclers require cloth that is clean and free of contamination. The better the quality of input feed, the more cost effective it would be to convert it to recyclable and reusable material. Participation in the circular textile cycle would also incentivise waste pickers into collecting and handling textile waste without sending it to landfills/ dump yards.
Way forward
There are several citizen level initiatives around Clothes Swap such as Green Stitched, Exchange Room, This for That, Sumrux etc, and many other upscaling projects. But the need of the hour is Extended Producer Responsibility (EPR).
EPR imposed on textile manufacturers would incentivise recovery of the harder to manage cloth waste—from collection, sorting, recycling or end of life solutions, while providing fair, liveable wages to those engaged in collection and segregation.
However, till such policy is introduced, it is recommended that synthetic fabrics (such as polyester, acrylic, nylon, spandex and acetate) that are all made from non-renewable fossil fuels be included in the Plastic Waste Management Rules, 2016 (as amended) thus making it mandatory for producers to accept the responsibility for non-recyclable cloth material. This will promote investment in research on alternative materials, reduce use of petroleum and induce producers and brand owners to take responsibility at the end of the product’s cycle.
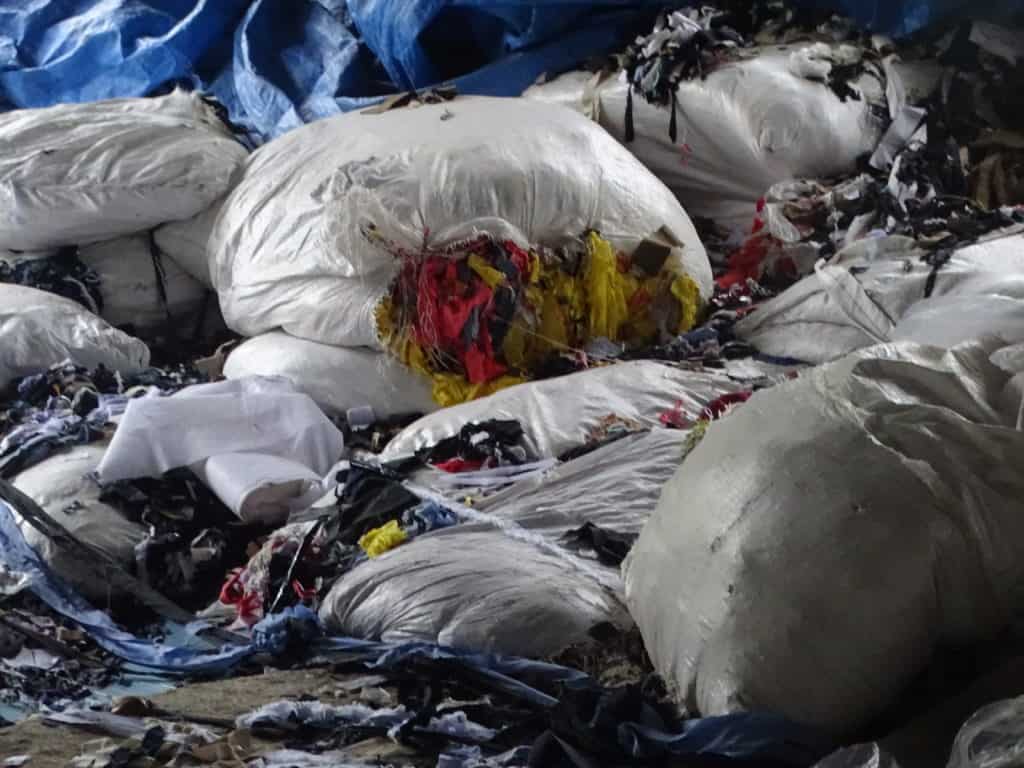
“You will find some industries converting PET bottles into yarn and claiming that they are taking up responsibility, but if you dig deeper, you will understand that converting PET into yarn is actually a bit of an eyewash,” says Myriam Shankar, Founder, The Anonymous Indian Charitable Trust.
Read more: Let’s not waste ‘waste’: In pursuit of the ideal waste management solution
What the waste industry has to deal with in terms of textiles is an endless list of different fabrics which cannot be recycled and have to be incinerated through co processing. And that too only along with materials which have a higher calorific value. So as a waste processing manager you have a material that no one wants, no one wants to pay for transport to the coprocessing plant, which also doesn’t really want this because of its very low calorific value.
In other words, the end of life of textiles is creating a huge cost that no one is bearing right now, other than DWCCs, who are already struggling with operational expenses. Only strict EPR in which these textile industries take back or pay for storage or own the end of life costs will this very problematic material be treated in a more sustainable manner.
The second important aspect is the availability of data on the quantity and composition of material/garments; quantity of textile waste in the dry waste streams and data on discarded textile imports. It is also important to map the textile recycling value chain across the country and plan for accessible infrastructure and capacities of waste handlers, collectors, sorters, and recyclers. And identifying and establishing necessary market linkages alongside raising consumer awareness.
With inputs from Shekar Prabhakar, Karthik Natarajan, Indha Mahoor, Vishwanath C, Akbar A and Aishwarya. Special thanks to Beula Anthony, for transcribing the interviews.